Read this article in French German Portuguese Spanish
US firm selected for work at ‘world’s first’ renewable hydrogen-based steel mill
16 February 2024
Sweden-based H2 Green Steel chose American firm Fluor Corporation – a multinational engineering and construction company – for work on a new plant dubbed the ‘world’s first renewable hydrogen-based integrated steel mill’
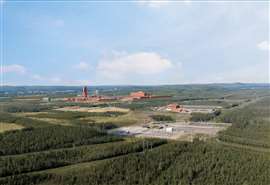
Fluor will provide engineering, procurement, and construction management services for H2 Green Steel’s plant in Boden, Sweden. They will focus on providing services to the site’s melt shop and casting, rolling, and finishing facilities.
The project started in 2021 and, since then, H2 Green Steel has actively been building partnerships and signing work contracts for construction and in anticipation of steel production (slated as early as 2025).
The original price-point for the project was announced at roughly €2.5 billion (US$2.7 billion) but has since more than doubled.
Power will be supplied on-site from one of the world’s largest electrolyser hydrogen plants, which is part of the roughly €6.5 billion (US$7 billion) project.
H2 Green Steel recently announced that they had secured a loan in that amount from more than 20 lenders including Svensk Exportkredit and the European Investment Bank (EIB) together with commercial banks BNP Paribas, ING, KfW IPEX-Bank, Societe Generale, and UniCredit.
According to H2 Green Steel, the site – once complete – will produce “five million tonnes of steel annually by 2030 with up to 95% less CO2 emissions compared to steel produced using traditional blast furnace technology.”
Thomas Östros, VP of EIB, said the project was vital to the bank and continent’s economy. “The steel industry is a strategic sector, being at the heart of the EU economy,” he said in a statement released last month.
“Our commitment to reach net zero by 2050 requires this sector to undergo transformative changes. It is important that the EIB, as the EU climate bank, is supporting H2 Green Steel in its pioneering development for a breakthrough clean technology to produce low carbon primary flat steel products. The project paves the way for the development of environmentally friendly steel - crucial for the decarbonisation efforts of the so-called ‘hard to abate sectors’, of which steel is an important one.”
Construction on the Boden plant is currently underway.
“The execution of the H2 Green Steel project will build on Fluor’s long-term presence in the steel industry, our expertise in novel, low-emissions steelmaking technologies and our strong presence in Europe,” said Harish Jammula, president of Fluor’s mining and metals business line.
What is ‘green steel’ and can it reduce carbon emissions?
The term green steel does not have a singular, official, or agreed-upon definition, though it is understood in the industry to be steel developed and produced through a process that does not use fossil fuels. In other words, the product itself is not made of less carbon, but the method to create it has a lower or near-zero CO2 emissions.
“Steelmaking is a very energy intensive process, and the current technology is mostly based on coal,” stated a report from financial institute ING. “Today, it accounts for 2.7 billion tons of CO2 every year, which represents 7% of yearly emissions globally. The shares are roughly doubled to 15%, 14%, and 12% for China, South Korea, and Japan, respectively.”
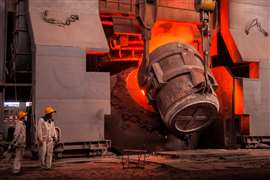
And steel usage globally is overwhelmingly within the construction industry. Data provided by the World Steel Association and BloombergNEF shows that most steel is produced for the sector: 51% of the world’s steel goes into buildings and infrastructure while 15% is used in mechanical equipment.
But early returns – regarding carbon reduction – on green steel seem promising, and it’s largely due to a slight tweak to a tried-and-true process: direct-reduced iron (DRI) production.
As is the case in Boden, hydrogen will be used to react directly with iron ore, which produces DRI (which in turn can be electrically heated to create steel). In the DRI process, iron and water are produced as byproducts as opposed to iron and CO2. The DRI procedure is already used with natural gas but, when gas is replaced with hydrogen, the process produces no greenhouse gases.
DRI steel using hydrogen power, science and data suggests, is definitely emitting less CO2.
What are the problems with green steel?
However, there are other hurdles to conquer.
According to ING, green steel is roughly twice the price of conventionally-produced steel. Added to it, the product itself is unproven and some in opposition to green steel production question if it will meet standards for construction and safety.
“Greener alternatives still have to prove themselves and are often viewed as prohibitively expensive in a highly competitive market,” noted ING. “Thoroughly transforming production processes takes years, so change is often desperately slow.”
According to US-based investment firm Franklin Templeton Institute, the green steel/hydrogen segment will require a global investment of $2.8 trillion to reach sustainability goals.
Furthermore, the DRI technique requires higher-quality iron ore, which is produced mostly in Australia, Brazil, Canada, and Russia. This will be convienent for green steel projects in those countries and regions, but it might make shipping costs unrealistic for some firms looking to transition from conventional to hydrogen-powered steel manufacturing.
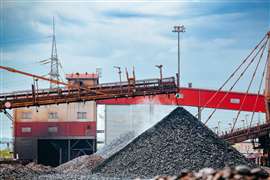
Despite caveats, green steel is poised to grow
Still, the International Energy Administration, in its 2020 Iron and Steel Technology Roadmap, forecast that electrolyser capacity will increase in the coming decade with new plants going up in Australia, Europe and the US.
With a global focus and gelling interests between investors, energy providers, governmental bodies, and contractors, green steel just might deliver on long-term promises of CO2 reduction industry-wide.
Coupled with dozens of countries’ net-zero emissions initiatives, demand for sustainable products is expected to rise, and green steel should be well-positioned to find a foothold among its competitors.
“Hydrogen coupled with electrification is the ultimate form of green steelmaking in a net zero economy,” said ING, adding that, for now, the development of DRI systems using gas is still a net-positive for emission reduction. “We do believe that gas-based steelmaking will act as an intermediate technology and could be a stepping stone towards hydrogen-based steelmaking.
“In fact, the latest gas-based steel mills are often dual fuel plants which can switch from gas to hydrogen easily once green hydrogen is abundantly available in the future.
Experts believe that this could be the case from 2035 onwards.”
CONTÁCTESE CON EL EQUIPO
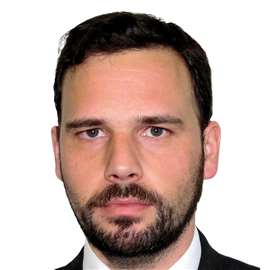