TPPL batteries in material handling applications: today and tomorrow
18 February 2024
Thin plate pure lead (TPPL) batteries are still in use for motive power in electric forklifts. But will that always be the case? Max Khabur of OneCharge takes a look.
When one thinks of the motive power behind any electric vehicle, lithium batteries immediately come to mind. One of the challenges equipment OEMs sometimes face in using them, however, is their higher price. In material handling applications, however — specifically forklifts — this is a disadvantage, especially for smaller fleets.
An alternative that remains in use for electric forklift fleets is the thin plate pure lead (TPPL) battery — still among the most advanced battery technologies for use in such equipment.
TPPL 101
As with all lead-acid batteries, TPPL technology consists of lead plates suspended in an electrolyte solution of water and sulfuric acid within a casing. However, TPPL plates are especially thin, allowing for more plates in the battery and a larger reactive surface area. The result is lower internal resistance, smaller energy losses, faster recharging and higher current delivery with lower voltage drop than a regular flooded lead-acid (FLA) battery.
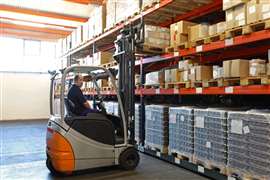
Compared to FLA technology, TPPL batteries — which are themselves improved versions of absorbent glass mat (AGM) batteries — offer additional advantages. For example, they are sealed batteries and thus don’t require regular maintenance. Gas emissions are also reduced. Finally, cycle life is longer, especially when the batteries are subjected to repeated micro cycles of discharging followed by partial-opportunity charging.
Drawbacks vs. Lithium
Nevertheless, even with the most recent improvements, TPPL batteries have drawbacks when compared to lithium batteries. First, TPPL units fall behind in energy density. The lead plates account for an estimated 40 - 60 percent of the battery’s weight, resulting in lower energy density. As such, for demanding applications in which more energy is needed to keep multi-shift operations running smoothly on a single battery pack, TPPL batteries cannot compete with their lithium counterparts.
TPPL batteries also experience sharp decreases in electrical conductivity at extreme temperatures. The electrical conductivity of the sulfuric acid solution drops dramatically above 90°F (32°C) and below 60°F (15°C). The maximum conductivity of a TPPL battery at -6°F (-21°C) is half the conductivity compared to when the electrolyte temperature is 60°F (15°C).
Finally, the preferred depth of discharge (DOD) for a TPPL battery is only 50 percent, with a maximum safe discharge of 80 percent. This is due to the formation of lead(II) sulfate on the electrodes during discharge. Instead of loose, fine crystals, the lead(II) sulfate forms a continuous dense layer of large crystals on the electrode surface. This can increase the volume of the plates significantly with deep discharge, which could lead to deformation and destruction of the plates.
Enhancing TPPL Performance
There are, however, several ways in which the design of TPPL batteries may be improved in the future to enhance their performance. For instance, the electrical capacity of the battery could be increased via changes to the electrode plate design and the use of powders to increase the electrolyte-electrode contact surface.
Additionally, the use of lighter materials may significantly decrease plate weight and therefore increase specific energy. Titanium, for instance, is 2.5 times lighter than lead as well as corrosion-resistant, and some research is being done into its use in the positive electrode of lead-acid batteries.
Carbon may also be used as an additive for plate coatings in both positive and negative electrodes to help prevent the formation of lead(II) sulfate while increasing the proportion of the electrode mass involved in reactions.
The main constraint for all three of these opportunities is the cost of production. Adding complex and expensive components could make TPPL products unreasonably expensive. This is a concern, as the prices of lithium batteries are expected to decrease with scale.
Outlook vs. Lithium
Thus, the future for lead batteries in material handling applications remains to be seen. Some predictions show it losing share to lithium batteries. In June 2022, EUROBAT, the association of European automotive and industrial battery manufacturers, published version 2.0 of its Battery Innovation Roadmap 2030. At that time, it said lead batteries for motive power in material handling, such as in forklift applications, had about a 90 percent share of the market, with lithium only beginning to make inroads. By 2030, the organizations sees lithium-ion batteries share of the motive power market growing to nearly 50 percent.
CONTÁCTESE CON EL EQUIPO
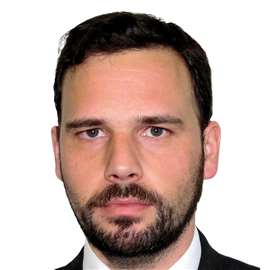