How are large excavators evolving?
20 November 2024
In the construction machine industry, few ‘little siblings’ get more attention than mini excavators but, as Mitchell Keller reports, innovation abounds in the medium and larger models.
Compact excavators are outselling their larger counterparts (by a big margin), and have been for years; in 2023, 365,000 mini excavators sold globally for a value more than US$12.5 billion, according to construction consultancy Off-Highway Research (OHR).
OHR estimates that North American mini hydraulic excavator sales grew 133% from 2014 to 2023, while the 6-tonne to 12-tonne range represented about 33% of the regional market share in 2023 (compared to just 2.6% ten years ago). The sales growth rates are similar in other major construction equipment markets like China and Europe.
It’s impressive data, but why should the little guys get all the love? While medium and larger machines may not move as many units, higher tonnage excavators are still modernising with the rest of the industry. And – with global megaproject volume on the rise – the demand for them is not going to diminish.
The bigger the better
Minis make their living in urban environments and confined spaces, lending to their popularity in recent years as major metros invest historic amounts into housing and infrastructure.
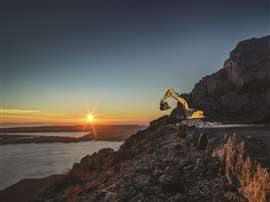
But midi and maxi (10-tonne and more) excavators shine in the world’s harshest environments; ideal applications for 10-tonne excavators and above include remote sites, mining, quarrying, and regions where climate and temperatures reach extremes.
That’s precisely what UK-based OEM JCB had in mind while developing its 370X excavator, which was released this year. Perhaps one of the most recognisable excavator manufacturers in the European market, JCB said its newest machine is its biggest X Series tracked excavator, yet – it launched the X Series range in 2018.
It weighs up to 40 tonnes and is backed by an 8.9-litre, six-cylinder Cummins L9 diesel engine that runs up to 240kW or 322hp at 1,700rpm. Its hydraulic system uses Kawasaki pumps and a new-generation KYB valve block.
JCB noted that weather was a vital component considered in developing the machine. “The 370X is designed to work in the harshest environment and has been rigorously tested to perform at its best no matter the climate,” says the company.
It also features a heavier counterweight for added stability, larger structures to cope with additional forces, increased service pipework diameters and raised hydraulic pressures for more power at the dig end.
Size also translates to increased productivity: the 370X can move 4.5 tonnes more material per litre of fuel and 86 tonnes per-hour more material than competitors, according to JCB’s testing. The diameter of the unit’s bucket was also increased to as much as 100mm with an attachment, which could also be beneficial on larger demolition jobs.
Increasing productivity
Electric machines, too, are sizing-up and entering new markets. Sweden-based Volvo Construction Equipment (Volco CE) released its EC230 electric excavator in Japan in May, having first released it commercially in North America and Europe.
Volvo CE believes the EC230 is now the ‘largest electric excavator available in Japan’. The commercial launch in the country was strategic, says Shoji Isamu – head of the Japan market at Volvo CE – noting the drivers of an electric midi excavator market.
“There’s significant customer interest in Japan for electric construction machines that produce zero emissions,” he says, noting dealers and end-users are needing “sustainable options that serve the needs of the Japanese market.”
Initially, five EC230s were delivered for the rental market, with two already scheduled for use as of the launch and a sixth to be ordered for a ‘major contractor’ working on multiple projects.
And among the very largest of large excavators comes Komatsu’s PC9000 hydraulic mining excavator for surface applications.
Developed by Komatsu Germany Mining Division (KGM) and Canada-based SMS Equipment (a subsidiary of Japan-based Sumitomo Corporation), Komatsu said of the new model, “The PC9000 is designed to increase productivity, performance and efficiency on the mine site. It is optimised to suit Komatsu’s 830E through 980E mining truck sizes, improving cycle times and lowering the overall cost-per-ton of material moved.”
The first machine was delivered to Fort Hills oil sand slurry mine in Alberta, Canada, a Suncor operation, along with 23 of Komatsu’s 980 haulers. The Canadian energy firm Suncor said the site extracts 194,000 barrels of material per day and has a life expectancy through 2068.
Komatsu’s mammoth PC9000 includes a larger bucket and elevated digging forces, installed to improve efficiency and cycle times.
Tuning-up technology and power
Autonomous features like grading assist, new sensing and camera technology, and telematics have already become the norm for most machines new to market.
In the coming years, fine-tuning electrohydraulic control systems, automation features and introducing more remote-operation opportunities will be the next breakthroughs for construction’s excavators.
Caterpillar’s Cat Command remote operation system is one example of how technology can allow operators to get out of the cab and continue their work, which could be particularly beneficial when digging around utilities or underground infrastructure.
The company demonstrated a remote excavator at the Edwards, Illinois, US, Caterpillar training and research facility during the company’s annual Technology and Construction Days.
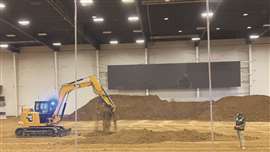
“It’s super-simple,” says the operator during an indoor demo at Edwards, standing with a Cat Command ‘belly box’ around his neck. It’s the device he uses to control a Cat 308 excavator, which is roughly 10m in front of him.
“When I switch over to dig mode, it’s going to be just like it was if I was in the cab,” he adds. “The right hand is going to be my bucket and boom, and my left hand is going to be my swing and my stick… very familiar.”
Caterpillar also released Cat Grade with 3D for excavators, which allows operators to grade complex designs across multiple machines using GNSS technology and RTK (real time kinematic) positioning guidance. It’s compatible with major surveying and scanning companies like Trimble, Topcon and Leica.
Alternative energy
Technology fuel innovations are also driving the excavator industry and Liebherr is leaving no stones unturned.
“The energy conversion technologies include a complete programme of highly efficient engines and drives, some of which are developed and produced by Liebherr itself: conventional combustion engines, hydrogen combustion engines, electric motors, fuel cells, batteries or hybrid drives,” Marc Wiedemann from Liebherr Kirchdorf tells International Construction.
Each technology has its strengths and weaknesses, and each requires a specific infrastructure, he explains. That means each is suited to different types of application.
“There is no one-fits-all drive technology for heterogeneous fields of application such as construction machines and cranes in the foreseeable future,” adds Wiedemann.
“Instead, the more precisely drive technology, application and region of use are harmonised, the greater the contribution to both customer value creation and climate neutrality.”
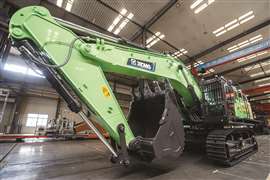
Some tech advances help illustrate the needs of the machine – a vital component when managing a robust fleet with a lot of working parts. At China-based OEM XCMG, the XE690DK hydraulic excavator has additional monitoring capabilities, which the company tells International Construction can enhance safety and efficiency.
“The machine is equipped with a split independent intelligent temperature sensing control system, which optimises fluid temperature control, reduces noise, and enhances overall efficiency,” says the OEM. “Additionally, the machine’s intelligent management system, which integrates IoT technology and a convenient mobile app, allows for real-time monitoring of machine status, ensuring operational safety and efficiency.”
Cabins you can live in
Perhaps the biggest change in excavators in the last decade is just how comfortable they are today.
Electrohydraulic components have reduced operator’s physical demands on the joystick, while some once-luxury features like air conditioning and ergonomic seating are becoming standard with most large brands.
A big reason for that is the global labour shortage, particularly among heavy machine operators. As a large section of the workforce retires, the industry is finding fewer members of younger generations interested in the profession.
Jason Hurdis, a global market professional with Caterpillar, tells International Construction that cabin comfort is a huge priority for the company. In May, at an outdoor demonstration at Caterpillar’s Edwards facility during peak summer heat, Hurdis admits he was sweating through his narration of the demo while operators “were in air conditioning” inside excavator cabins “making fun of me on my headset.”
Hurdis is in on the joke, though; this is years of work developing new cabs coming to fruition, and he welcomes the gentle ribbing from operators because it means they’re enjoying their work.
Hurdis adds that simple changes like improved LED lighting and access to radio control (for operators to play their own music) are small on paper but huge for the workers.
“That operator gets in at 6 a.m. in the morning, and he or she may not get out of that cab until four or five o’clock in the afternoon,” says Hurdis. “The more comfortable we can make it – reclining seats, air conditioning, good visibility – the less fatigue they’re going to have.”
Chinese OEM LiuGong tells International Construction they, too, are focused on safety and cabin improvements. Their 925FCR cab includes seven new factory-available features including a parallel wiper (for high-dust scenarios), a tilting pod to improve ease of access and egress for operators, a 10.1” display that shows 360-degree visibility, USB A and C charging ports, upgraded audio and radio, improved seating and hydraulic adjustments.
“The electro-hydraulic system ensures fast communication between joysticks, pumps and valves resulting in precise control across the power range,” says LiuGong. “Furthermore, LiuGong have now added the ability for operators to adjust hydraulic priorities, hydraulic response and joystick sensitivities.”
Advancing every detail
Even though remote-control operation, 3D-grade assist, and electrohydraulic systems might seem like cutting-edge tech (and they are), excavators have been around a long while, and a lot of these major technology features have been around, too.
While these have improved to an impeccable level today, Justin Steger – product marketing manager for John Deere’s excavator division – says his team are making a point not to overlook some of the basics.
Referencing Deere’s 210 to 380 model excavators in its newer P-series (compared to its prior G-series), Steger says the OEM is still discovering design and access innovations that can improve productivity without a computer chip or emerging technology.
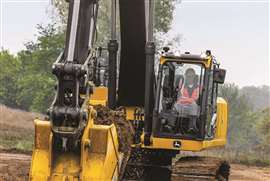
“We made it easier to grease joints in general, but specifically that stick-to-bucket joint,” explains Steger. “We have a grease channel that comes from the centre out, and the thought there is you can send grease in from the middle outwards, and it’s going to take that dirt and debris out with it and eliminate any accelerated wear in those bushings in that joint.”
Steger says Deere also made hardier its already sturdy top-hat bushing and hardened pin for the stick-to-bucket joint.
“Between the bushing being harder, the pin being harder, and the seal being better, we’re seeing two-to-three times the life compared to the previous G-series design of that joint,” adds Steger.
Components as simple as fans – for cooling engine, hydraulics and electric parts – have been reconsidered by Deere, and Steger says the results have been inspiring more advanced tinkering.
“We’ve gone from our G-series’ hydraulically-driven fans, now with the P-series we have our electronic on-demand cooling fans,” he explains. “We’re actually seeing a minimum 7% – more likely 10%-plus – fuel savings depending on the application.”
Steger says all these adjustments come down to a single desire: creating value for owners and end-users. “Anytime we can free up some power, reduce that engine load, we reap the rewards, and our customers reap the rewards in fuel savings,” he says.
It may take some years before larger excavators make the giant leap in fuel technology but until then the industry seems geared to extract efficiencies from modern excavators.
CONTÁCTESE CON EL EQUIPO
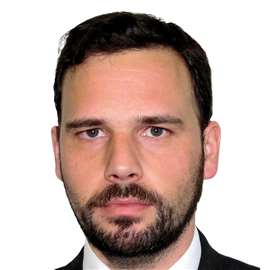