¿Qué innovaciones ‘concretas’ están dando forma al futuro?
21 March 2024
El material constructivo más utilizado en el planeta ha evolucionado a lo largo de milenios, pero la próxima década de innovaciones será clave para que la industria cumpla sus ambiciosos objetivos de sostenibilidad, informa Mitchell Keller.
“Cuando la gente me pregunta a qué me dedico… mi respuesta es: ‘¿Has visto Los Picapiedra?’”, dice Joel Galassini, vicepresidente ejecutivo de la división de cemento comercial de Cemex, una empresa de materiales de construcción con sede en México.
Los Picapiedra es una caricatura estadounidense de la década de 1960 ambientada en una Edad de Piedra romántica.
Su respuesta jocosa sugiere que el sector en el que trabaja está pasado de moda.
“Me describo como una caricatura de la Edad de Piedra, pero tenemos mucha gente que son los Supersónicos”, añade.
Los Supersónicos fueron los personajes principales de otra comedia animada estadounidense (llamada simplemente Los Supersónicos) de los años 60, que seguía a una familia en un escenario idealizado del futuro.
Un sector en evolución
Justo encima del hombro de Galassini, mientras cuenta esta anécdota, se encuentra el lote sur del Centro de Convenciones de Las Vegas; repleto de sofisticados equipos de construcción, tecnología y ciencia de última generación en exhibición para World of Concrete 2024.
Ha tomado tiempo, afirmó el vicepresidente de Cemex, pero cree que la industria del concreto está dando pasos agigantados hacia el futuro.
“Estamos usando IA en muchas de nuestras operaciones, manejamos drones y observamos vehículos autónomos y todas esas cosas... Lo describo como Los Picapiedra pero, en realidad, tenemos muchos ‘Jetsonianos’. cosas que están pasando”, dijo.
Soluciones bajas en carbono
Ya sea impulsada por misiones internas de la empresa, regulaciones gubernamentales o estipulaciones contractuales, la industria del hormigón ha necesitado dar grandes pasos, rápidamente, para crear más productos a partir de materiales reciclados con menores huellas de CO2.

Para satisfacer la demanda de los consumidores y cumplir con las estipulaciones ambientales, muchas empresas reconfiguraron su proceso de fabricación de cemento. El cemento es un ingrediente clave del hormigón, pero uno de los principales productores de carbono del mundo.
Esto ha significado una mayor participación de la comunidad científica, que a nivel mundial ha encontrado soluciones con bajas emisiones de carbono para mezclas de cemento, incluidos investigadores de Empa, los Laboratorios Federales Suizos para Ciencia y Tecnología de Materiales.
“Las principales innovaciones en cemento y productos de hormigón de los últimos años han sido impulsadas por la necesidad de mejorar la sostenibilidad y reducir las emisiones”, confirmó el Dr. Mateusz Wyrzykowski, líder del grupo de tecnología del hormigón en el Laboratorio de Hormigón y Asfalto de Empa.
Todo, desde grafeno, cáñamo, café y una gran cantidad de nuevos aditivos y sintéticos especializados, se han abierto camino en el hormigón y el cemento. Los resultados y la intención varían, pero la experimentación es fundamental para descubrir productos innovadores que puedan ayudar a reducir las emisiones.
“Se han logrado avances significativos gracias a la reducción de residuos y al uso responsable de los recursos”, añade Wyrzykowski.
Uno de los materiales más intrigantes para el cemento que Empa ha estudiado es el ‘biocarbón’. Es un material rico en carbono creado a partir de la pirólisis de biomasa; en otras palabras, es el bioproducto de calentar materiales orgánicos sin oxígeno.
En teoría, a partir de materiales orgánicos, el hormigón elaborado con cemento de biocarbón podría eliminar el carbono de la atmósfera. En la actualidad, el biocarbón se ha utilizado con éxito como forma de aislamiento.
Algunos productos ya están en el mercado, pero Empa sugiere que próximamente se desarrollará una versión más fuerte y segura de un aditivo de biocarbón con investigaciones adicionales.

“El biocarbón es muy poroso. Absorbe mucha agua, pero también los costosos aditivos utilizados en la producción de hormigón”, explicó Wyrzykowski. “Es difícil de manejar y tampoco completamente inofensivo”.
Según Empa, el fino polvo de biocarbón es problemático para el tracto respiratorio humano y conlleva riesgo de explosión.
Por ello, se continúa investigando si el material se puede transformar en gránulos.
“Estos agregados ligeros ya existen a partir de otros materiales como la arcilla expandida o las cenizas volantes”, afirma Wyrzykowski, señalando algunos precedentes. “El conocimiento sobre el manejo de estos materiales está disponible en la industria, y esto aumenta las posibilidades de que el concepto se ponga en práctica”.
Reanálisis de la producción de cemento
De regreso a Cemex, Galassini dijo que su compañía ha fabricado productos con menos clinker que el cemento tradicional y productos con cenizas volantes, los cuales ayudan a reducir las emisiones de carbono.
Pero volver a analizar toda la producción de cemento, afirmó, es tan importante como ajustar su composición química.
“Quemamos cosas diferentes en nuestros hornos en lugar de carbón”, dice. “Podemos quemar productos de desecho reciclados. Podemos quemar neumáticos, podemos quemar combustible residual, podemos quemar desechos industriales y residenciales... Tenemos algunos de los cuales podemos tomar ganado, cadáveres de vacas y desecharlos de manera responsable y usarlos como combustible para los hornos”.
El sistema, señala, no está completamente exento de emisiones, pero éstas se reducen considerablemente y ayudan a facilitar mayores ganancias, incluido el ahorro de costos para las fuentes de combustible reciclado.

“Nuestra planta de cemento en Berlín consume un 98% de producto reciclado”, dice Gassalini, señalando que el país dejó de eliminar los vertederos a mediados de la década de 2000. “Tomamos todos esos desechos, los granulamos y los quemamos en el horno. Entonces, en lugar de tirarlo a un vertedero y generar metano, que creo que es 30 veces más potente que el CO2, podemos quemar esos desechos, crear cemento y crear un producto”.
Esta forma de pensar no está aislada; la mayoría de los principales actores mundiales han adoptado enfoques agresivos para reducir la producción de carbono y aumentar la circularidad.
El Heidelberg Materials Group de Alemania lanzó un conjunto de productos con bajas emisiones de carbono en 2023 y planea abrir una instalación de almacenamiento de captura de carbono (CSS) en una planta de cemento en Noruega para fines de 2024.
“Nuestro proyecto CSS en la planta noruega de Brevik comenzó como una idea ambiciosa a mediados de la década de 2000”, dijo un portavoz de Heidelberg.
“Las ideas iniciales maduraron hasta convertirse en un estudio documental. En diciembre de 2020, el gobierno noruego dio la aprobación final y apoyó la construcción de la primera instalación de captura de carbono a escala industrial del mundo en una planta de cemento”.
Este proyecto eliminaría el carbono del sitio y lo depositaría en un casillero submarino.
“Una vez en funcionamiento, se capturarán 400.000 toneladas de CO₂ al año y se transportarán por barco a una terminal terrestre en la costa oeste de Noruega”, explicó Heidelberg. “Desde allí, el CO₂ licuado se transportará por tubería hasta el lugar de almacenamiento bajo el Mar del Norte, donde se almacenará de forma permanente”.
Si bien los métodos de captura y secuestro de carbono aún son imperfectos, Heidelberg señaló que son sólo una palanca de innovación sostenible.
“Continuamos descarbonizando nuestra cartera de productos a través de medidas convencionales de reducción de carbono”, afirmó la empresa. “Durante años, nuestros equipos han estado trabajando para reducir el contenido de clinker en nuestros productos, cambiar la cartera de productos y aumentar la proporción de combustibles alternativos”.
Las máquinas ayudan a la innovación
Mientras el hormigón y el cemento experimentan cambios físicos, la maquinaria que mezcla y vierte la sustancia también debe mantenerse al día.
Los camiones mezcladores volumétricos o móviles no son nuevos, pero los avances en la tecnología informática, el almacenamiento de materiales y la catalogación de datos han hecho que estas herramientas, ya de por sí valiosas, lo sean inmensamente en la era moderna.

Cemen Tech se autodenomina el mayor fabricante del mundo de soluciones de dosificación volumétrica y mezcla continua de concreto y ha estado en el juego de la mezcla volumétrica desde el principio.
Con todos los materiales de concreto necesarios almacenados y mezclados en el camión y en el sitio, los gerentes de proyecto pregonan ahorros en transporte, pero la sofisticada tecnología de la unidad también garantiza que el desperdicio sea limitado y que la producción de concreto cumpla con las expectativas para el trabajo y el clima.
Zach McQuay, que dirige McQuay Construction en Oklahoma, EE. UU., utiliza una Cemen Tech C-Series y observa el orden que una máquina puede aportar a un trabajo.
“Tienes el control total sobre ello”, dice. “Es una planta dosificadora móvil, por lo que no tenemos tiempo de conducción. Podemos cargar todo el material en el sitio y recorremos 402 m (440 yardas) por día con solo tres camiones”.
En comparación con el uso de una planta de premezclado fuera del sitio, McQuay estimó que un trabajo similar requeriría 20 o más camiones, más el tiempo de viaje y carga y descarga.
Con una mezcladora volumétrica, McQuay dice: “No produciremos concreto hasta que presionemos ‘Iniciar’. Recibimos concreto fresco a pedido”.
Las pruebas de aire pueden realizarse en el sitio y el mezclador puede crear lotes pequeños a la vez, lo que, según McQuay, reduce el desperdicio.
“En el mundo del concreto premezclado, si no pasan la prueba de aire, se rechaza toda la carga”, explicó, señalando que las mezcladoras volumétricas pueden simplemente hacer un nuevo lote (y hacer ajustes a la mezcla intermedia). “En el mundo volumétrico, si estropeamos esa prueba de aire, tendremos menos de media carretilla para reciclar”.
Con arena, roca, agua, productos químicos y sintéticos necesarios para producir concreto en el camión, una interfaz de computadora permite a los usuarios administrar la composición exacta de su mezcla y ajustarla según sea necesario.
“Tenemos una relación agua viva/cemento. Tenemos una tasa de dosificación en vivo de nuestros químicos. Tenemos una clasificación en vivo de nuestra arena, roca y agua, por lo que podemos marcar cualquiera de esos aspectos en cualquier momento durante el proyecto”, agregó McQuay.

El registro de datos crea una red de información confiable que los adoquines o capas podrían recuperar para trabajos similares o en entornos comparables.
En otros lugares, los avances en inteligencia artificial, escaneo e impresión 3D y tecnología de sensores han ayudado enormemente a los adoquines y otras máquinas centradas en el concreto. Un ejemplo de ello es una extendedora de encofrado deslizante del grupo alemán Wirtgen.
“Al extender hormigón con las extendedoras de encofrado deslizante de Wirtgen se pueden utilizar diferentes funciones automáticas, como el sistema AutoPilot 2.0 o el insertador automático de pasadores”, explica la empresa. “El sistema de control AutoPilot 3D desarrollado por Wirtgen sirve para controlar con precisión y sin hilos las extendedoras de encofrado deslizante al crear todo tipo de perfiles desplazados y encajados.
“Ya no es necesaria la creación de un modelo de datos geodésicos por parte de un topógrafo. El montaje y desmontaje de un cable, como es habitual en un sistema de control de máquina convencional, está obsoleto.
“La máquina se mueve a lo largo de una línea virtual con guía de posicionamiento por satélite. Tanto el ajuste de altura como la dirección de la máquina se controlan automáticamente”.
Impresión 3D y hormigón
Uno de los avances en automatización del hormigón más tentadores y visualmente estimulantes es la impresión 3D.
Las máquinas de impresión 3D de extrusión de capas, que utilizan una boquilla controlada que exprime con precisión una pasta de cemento capa por capa, fueron algunas de las demostraciones más populares en World of Concrete.
Las pilas de hormigón, que parecen pasta de dientes, se pueden construir tan alto como lo permita la impresora o el entorno, y algunas impresoras son lo suficientemente grandes como para imprimir edificios enteros.

Una impresora 3D de COBOD International, un producto con sede en Dinamarca, completó el año pasado lo que se dice que es el edificio impreso en 3D más grande de Europa en Heidelberg, Alemania. El edificio tiene 54 m de largo, 11 m de ancho y 9 m de alto.
La impresora 3D COBOD BOD2 puede crear formas geométricas no cuadradas además de estructuras en caja. La construcción comenzó a mediados de 2023 y tardó aproximadamente 172 horas.
“Esperamos que las impresoras duren hasta cinco o diez años”, afirma Philip Lund-Nielsen, cofundador de COBOD, y señala que la longevidad de las máquinas está aumentando. “Es 90% acero galvanizado. La mayoría de los problemas que tienen nuestros clientes en el sitio es obtener los materiales correctos; una vez que dominan eso, se vuelven realmente eficientes”.
Poniendolo todo junto
Al igual que el concreto es un producto hecho de elementos particulares que trabajan en conjunto, los líderes de la industria necesitarán continuar trabajando en colaboración para hacer avanzar el producto.
“Se trata realmente de trabajar con propietarios, arquitectos e ingenieros para asegurarnos de que estamos diseñando una pieza de edificio, acera o pavimento correctamente y no sobrediseñándolo ”, dice Galassini. “Si observamos el concreto que se vierte en la mayoría de las aceras de una ciudad; es una receta especificada por la ciudad.
“Esa receta creará una acera que tiene, digamos, entre 6000 y 8000 PSI de resistencia, lo que sería similar a la pista de aterrizaje de un aeropuerto. Entonces puedo aterrizar un 747 en una acera que solo necesita 2500 PSI de fuerza”.
Con toda esta información y la tecnología disponible para abordar este ejemplo de ingeniería excesiva, Galassini cree que es hora de encontrar soluciones a largo plazo.
Y aquellos que no se modernicen y no ayuden a resolver el problema pueden quedarse atrás.
“Creo”, dice Galassini, “que las personas que continúan innovando e impulsando probablemente serán las ganadoras. En algún momento, las personas que se resisten al cambio estarán en un punto de inflexión en el que, de repente, no tendrán otras opciones, o tal vez sea demasiado tarde”.
CONTÁCTESE CON EL EQUIPO
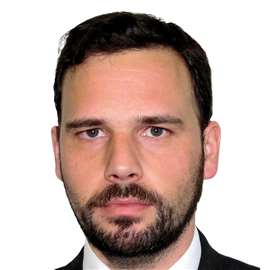