Grúas torre: Método modular
30 June 2020
Con el crecimiento de la construcción industrializada, el sector de grúas se vuelve aún más importante. De hecho, el izado de las piezas demanda grandes equipos de mucha capacidad de carga, por lo que generalmente las áreas urbanas exigen grúas torre en lugar de otros modelos, dado que éstas son instaladas en el sitio de construcción sin ocupar espacios en vías públicas.
Los productos prefabricados puede ser modelos bidimensionales, como muros, losas modulares, sistemas de piso, pero también los hay tridimensionales. Por ejemplo, hoy en día se utilizan elementos como escaleras o pozos de ascensor prefabricados, los que son provistos por fabricantes de piezas estructurales de hormigón o acero.
La nueva generación de las soluciones prefabricadas, en tanto, va un paso más allá de lo que hasta hoy el prefabricado pudo ofrecer. Con el sistema de Prefabricados Modulares Volumétricos, la modularización e industrialización de los edificios alcanzan niveles desconocidos hasta ahora. Y eso trae aún más importancia al sector de grúas para la instalación de estos elementos.
Básicamente, el sistema de prefabricados modulares volumétricos supone que toda la instalación de servicios e incluso de terminaciones de una unidad habitacional u oficina, vienen listos de fábrica. Cañerías, conexiones eléctricas, fijaciones, ventanales, servicios y otros elementos son instalados antes del montaje.
VENTAJAS
Ahorros de tiempo. El más evidente beneficio del método es ahorrar tiempo de construcción. La puesta en marcha del sitio de trabajo, el movimiento de tierra y las fundaciones pueden hacerse simultáneamente con la fabricación de los módulos en otro lugar. Un hotel de seis pisos, por ejemplo, puede fabricarse en tres meses y montarse en solamente 20 días en el sitio. Este tiempo ahorrado trae beneficios financieros, dado que el retorno de la inversión es más rápido.
Calidad asegurada. Retrasos típicos por las condiciones climáticas no afectan la construcción de los módulos en la fábrica. Además, la producción en línea e incluso robotizada pueden llevar este tipo de construcción al estándar de productividad actual.
Seguridad. Mientras más partes de la construcción se dan fuera del sitio, son menos las horas trabajadas en altura.
Reducción del tráfico. La construcción modular puede reducir el número de entregas de material al sitio en hasta un 90%, y reduce la distancia promedio de desplazamientos de trabajadores en hasta un 75%.
Superación de problemas de reclutamiento. Hasta un 80% de las actividades laborales tradicionales pueden realizarse en la fábrica de los módulos. Para esta fuerza de trabajo el desplazamiento es igual, no importando donde sea la obra, pero son menos los especialistas que deben desplazarse a instalar los módulos, siendo además trabajadores más calificados.
Reducción de ruidos, polvo y CO2 en el sitio de trabajo. La fase de construcción en sitio se reduce, tal como se disminuye el uso de equipos pesados. Grúas torre eléctricas para el montaje de los módulos minimizan el ruido y la contaminación, beneficiando a vecinos y el ambiente.
Reducción de desechos. La construcción modular puede reducir a la mitad los desechos, en comparación con la construcción convencional. Los módulos entregados y prontamente suspendidos reducen además la necesidad de espacio de almacenamiento de material.
Sustentabilidad. Cerca del 90% del proceso de producción de los módulos en fábrica tiene un gran potencial para la fabricación limpia, reduciendo las emisiones de gases durante la fabricación, afectando positivamente todo el ciclo de vida del edificio.
COSTOS
Restricciones de transporte. Regulaciones viales restrictivas, permisos especiales de carga y posibles restricciones espaciales en ciudades menores imponen algunos límites económicos al sistema. Por lo general, los módulos tienen dimensiones cercanas a 3,4 metros de ancho, 3,2 metros de alto y 12 metros de largo. El peso máximo es de entre 30 y 40 toneladas cortas (del inglés short ton) es una unidad a 907,185 kilogramos). El transporte representa cerca del 20% del costo del sistema, y tiende a ser más.
Dimensión de la grúa. Grúas superiores a seis pisos son las preferidas, debido al espacio de erección. Son dos los sistemas de prefabricados modulares volumétricos que se utilizan generalmente. El peso de las unidades en acero varía entre 8 y 20 toneladas cortas, mientras que las unidades hechas en hormigón varían entre 25 y 35 toneladas cortas. Los módulos de concreto son frecuentemente los preferidos en edificios residenciales debido a su durabilidad y facilidad de inspección. La tendencia por menores emisiones también en este método llevará al uso de materialidades híbridas y utilización de maderas ligeras, porque la producción de cemento es responsable por cerca del 5% de las emisiones globales de CO2.
Otro criterio importante será la elección de accesorios de izado utilizados y que son hechos a la medida para los módulos. Por tener características de auto equilibrarse, estos accesorios previenen la transmisión de fuerzas externas al módulo, y acomodan el centro de gravedad de cada módulo con precisión, de manera a facilitar su correcto posicionamiento. Por estas razones, los proyectos de prefabricados modulares volumétricos requieren de grúas torre de alta capacidad. La experiencia indica que el costo beneficio de aplicar grúas torre por arriba de las 30 toneladas cortas lleva a que esta sea la opción para un 15% del total de los proyectos. Pero, con recientes desarrollos dedicados a este sistema, contratistas de grúas podrán mantener los costos más fácilmente controlados.
VOCACIÓN
Los proyectos que pueden aprovechar el método de prefabricados modulares volumétricos para una mejor relación costo beneficio serán aquellos con mayor grado de repetición. Entre otros ejemplos de estructuras como estas, están los alojamientos estudiantiles, hoteles, torres residenciales y vivienda social.
La construcción modular prefabricada volumétrica puede ser una solución cuando hay escasa mano de obra, donde la construcción por medios convencionales sea cara y donde el tiempo de obra tiene que ser acotado, debido a carencias extremas de viviendas, por ejemplo. Países como Australia, Francia, Reino Unido y EE.UU., han anunciado la necesidad de un millón de unidades habitacionales que se debieran construir en 2020.
Los gobiernos de Australia, Singapur y Reino Unido están convirtiendo la construcción modular en prioridad estratégica. El Consejo de Desarrollo y Vivienda de Singapur (HDB) adoptó el método de prefabricado volumétrico de concreto para un 35% de los proyectos en 2019. En Australia, en tanto, el gobierno quiere crear “ciudades de veinte minutos”, que son llamadas así por el tiempo que idealmente sus habitantes requerirían para satisfacer sus necesidades diarias. Se incrementará el número de torres residenciales de mucha altura para reducir la huella de carbono. Y otros departamentos públicos en el mundo deberán seguir la tendencia, lo que aumentará la demanda de mercado por prefabricados modulares volumétricos.
Singapur es hoy en día el mayor escenario de pruebas del método. Mientras tanto, experiencias en otros países han impuesto desafíos para los equipos de izado. El edificio Habitat 67 en Montreal, Canadá, que forma parte de un complejo de convenciones y tiene 12 pisos, fue erigido en 1967 y da testimonio del potencial de la prefabricación. Los 354 módulos de hormigón, cada uno de 80 toneladas cortas, fueron posicionados usándose una grúa tipo Derrick montada sobre pedestal y movida en rieles de Dominion Bridge. Este equipo ofrecía 82 toneladas cortas de capacidad a un radio de 30,5 metros y de 100 toneladas cortas a un radio de 18,2 metros. A fin de nivelar los módulos de concreto en cada esquina del molde de izado Francon, una unidad hidráulica fue instalada en la punta del cable de izado.
También en 1967, otro proyecto de prefabricación modular volumétrica tuvo su inicio en San Antonio, Texas, con un diseño particularmente económico y un plazo notablemente corto de construcción. El hotel Hilton Palacio de Rio, con 22 pisos, fue entregado en solamente 10 meses. La construcción modular acortó el plazo que típicamente sería de dos años a tan solo nueve meses, con el mes adicional para terminaciones. Un total de 496 habitaciones fueron posicionadas en 46 días, usándose un Manitowoc 4000W. La grúa tenía una pluma personalizada de 82,3 metros, con 50 toneladas cortas de capacidad con top inclinado que aumentaba la altura de carga posible. Los módulos de 35 toneladas completamente terminados, incluso amoblados, fueron izados con precisión de 19mm, con el auxilio de un espaciador construido para el servicio con balanceador de sentido opuesto improvisado con un motor de helicóptero Sikorski.
El sistema funcionó tan bien que, en lugar de completar el posicionamiento de 10 módulos por día, los constructores terminaron por realizar la colocación de 35 al día, dando otro testimonio de la importancia que es tener el equipo de izado correcto para lograr el mejor beneficio de la construcción modular.
Hoy en día, el sistema de posicionamiento de los prefabricados modulares volumétricos usualmente utiliza personas jalando las cuerdas de orientación. Se trata de un método ineficiente, que demanda mucho trabajo humano y puede ser riesgoso. Pero, en lugar de sistemas de orientación como el motor de helicóptero usado años atrás, pueden servir nuevos dispositivos en base a giroscopios. Muchos productos que usan giroscopios para controlar la rotación de la carga y eliminar las cuerdas de orientación fueron lanzados en los últimos años. El fabricante de grúas japonés Kitagawa presentó uno, el Gyro-master. Por su parte, el separador modular de la serie Everest, del fabricante australiano Verton Group, utiliza un rotor de esfuerzo variable operado a distancia para ayudar a suspender cargas de hasta 1.500 toneladas cortas.
El control remoto ayuda a incrementar la seguridad general al remover los riggers de la zona de izado. El tiempo de ciclo se reduce en hasta un 25%, y menos riggers son demandados en el sitio.
Kitagawa ofrece unidades de capacidad de hasta 75 toneladas cortas, y en Japón ya existen algunas con capacidad de hasta 125 t. El equipo debe ser usado con un marco de izado con dispositivo de compensación para minimizar el tiempo de colocación de la carga en la posición exacta. Tal marco de entorno alrededor de la carga puede además ofrecer una variedad de puntos para las eslingas, lo que facilita un rigging que respeta las características estructurales del módulo prefabricado y mantiene su integridad. Con ello, también se hace innecesaria la organización de barras de separación con anchos crecientes mientras más cercanas de la carga, lo que suele demandar grúas con mayores alturas bajo el gancho.
INDICACIONES
Aunque cada sitio de trabajo demande su propio plan de elevación de materiales con aplicación de grúas, hay ciertas reglas generales para usar el método de prefabricados modulares volumétricos en edificaciones:
De ser posible, los camiones de entrega de los módulos deben descargarse cerca el edificio en construcción, y la grúa torre tiene que estar posicionada al centro del sitio, de manera a minimizar los radios de operación y la capacidad de carga que se hace necesaria. Diferente de los prefabricados de concreto tradicionales, los módulos volumétricos son en general muy grandes para su almacenamiento en el sitio. Una logística eficiente de transporte y entrega debe estar presente.
Para los módulos de concreto reforzado, es necesario pensar en una grúa con capacidad de entre 28 y 65 toneladas cortas, que con barra distribución del esfuerzo puedan trabajar en radios de 35 metros, dependiendo de la ubicación de la grúa y del formato del edificio. Para que se alcancen todas las extremidades del sitio de trabajo, la capacidad debe estar calculada en base la punta más externa de la pluma.
Los abatibles muestran su valor en sitios con fuerte restricción espacial. Pero, en la mayoría de los casos, las tradicionales grúas “cabeza de martillo” con largo de pluma reducido y adaptadas a las condiciones del sitio son más efectivas en términos económicos. Ellas son hasta un 40% más baratas de armar y consumen menos tiempo en el rig. Además, estas grúas producen menores fuerzas de reacción, consumen menos energía y simplifican la gestión de prevención de colisión.
Los modelos de torre flat top, en tanto, son preferibles en la mayoría de los casos, debido a su menor tiempo de instalación y menor peso total. Una grúa flat top presenta más facilidad para cambiar el largo de pluma y contrapluma, dado que no tiene tirantes.
La manipulación de los típicos módulos prefabricados volumétricos en general exige el máximo momento de carga durante la mayor parte del servicio. Usar el largo máximo de la pluma, por ende, significa que un solo carro será la mejor opción. Además, la utilización de la máxima extensión de pluma para posicionamiento del módulo es deseable. De manera que cuando se usa una grúa “cabeza de martillo” un solo carro es mejor que una configuración de doble carro, común en otras aplicaciones de grúas torre en servicios de levantamiento pesado.
El izado preciso es más crítico e importante que la velocidad. Sistemas de inversión de frecuencia para un prendido suave, con micro control del movimiento, ayuda mucho en estos casos. También es conveniente que la grúa tenga un sistema de cámaras para seguir de cerca el movimiento del gancho y el carrete de cable. Aplicar sensores de GPS en el marco de izado del módulo permite que información en tiempo real sea transmitida al software de control de la construcción. El almacenamiento de datos permite la investigación de toda la operación de la grúa por internet.
El nuevo método de construcción modular con prefabricados volumétricos abre grandes posibilidades para todos los que trabajan con grúas torre.
CONTÁCTESE CON EL EQUIPO
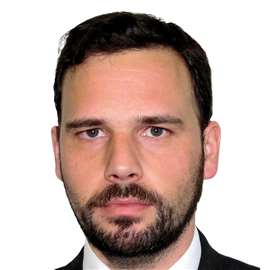