How Eiffage’s director of operational services plans to keep the company one step ahead
14 October 2024
As director of operational services at Eiffage Construction, Fabien Darchis is at the coal face of working out how one of Europe’s largest contractors can implement strict new French and European sustainability regulations into its every-day work. He tells Catrin Jones about the challenges - and opportunities - they bring.
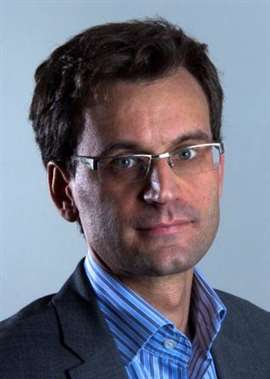
Fabien Darchis, director of operational services at Eiffage Construction, is a man with an eye for detail. He has to be.
As one of the key people responsible for working out how Eiffage’s thousands of domestic employees and subcontractors go about complying with France’s increasingly ambitious sustainability laws, Darchis has a lot to keep on top of.
Over the last few years, the French government has charged ahead of its European neighbours, passing a raft of new regulations which set aggressive targets for reducing carbon emissions of buildings and require construction companies to use more energy efficient materials and equipment.
The new laws go a long way towards fulfilling France’s obligations under the European Union’s Energy Performance in Buildings Directive - something most other European governments are still only thinking about.
For Eiffage, ranked number five on the CE100 list of the top European contractors, which is involved in some of the continent’s major engineering and construction projects, including the UK’s new high-speed rail project, Darchis says it’s important to stay ahead of the curve.
Is regulation driving sustainability in France?
“Since 2015, we have been operating within a regulatory perimeter in France that covers important areas such as carbon reduction in buildings, biodiversity, waste management, and more,” he says. “New laws are introduced every year, setting the trajectory for our sector in the years to come. For example, there’s a regulation called RE2020 that requires a significant reduction in the carbon footprint of our buildings.”
RE2020, also known as the Environmental Regulation 2020, aims to improve the environmental performance of buildings throughout their entire lifecycle, from the procurement of raw materials to construction, use of the facility, and even the building’s ‘end-of-life.’
In this way, the RE2020 goes beyond its predecessor (RT2012) and is pushing the construction industry to reduce its carbon footprint. The sector accounts for 44% of France’s energy consumption and nearly 25% of the country’s climate-damaging CO2 emissions.
The law, which took effect on January 1st, 2022, becomes increasingly stringent in 2025, 2028, and 2031 to ensure emissions go down.
For an industry which has already been in the grip of a Eurozone-wide construction slump since 2022, the results so far have been mixed. Boston Consulting Group estimates that the regulations have increased the cost of constructing a new building by 10-20%, helping to slow demand.
Nonetheless, Darchis says that Eiffage can benefit from a first mover advantage.
He says, the company can benefit from seeing how the new rules are helping to shape the wider construction market. He adds that market sectors developing in France include energy rehabilitation and the transformation of office spaces into housing.
“We know that all building permits submitted by 2025 will have to adhere to strict carbon emission standards, leading to a sharp drop in carbon footprint. This compels us to rethink and review our construction methods,” Darchis says.
“The advantage is having a clear perspective on how regulations will evolve over time, allowing us to project the future of construction in 2031 and beyond. There is considerable pressure from European and French regulatory legislation, impacting our company, Eiffage, and Eiffage Construction.”
To that end the company has drawn up an action plan focused taking on more low carbon, biodiversity, and reuse projects as well as thinking carefully about the way it goes about building - something the company can implement across its operations.
One example is the Olympic Village for the Paris 2024 Olympics which Eiffage is currently converting into housing following the Games this summer. The project is built with a 30% reduction in carbon compared to a typical French construction while 94% of the materials it used were recycled from other projects. And the project incorporates insulated facades, cooling floors and green spaces which it says will ensure a temperature difference of at least six degrees celcius compared with outdoor conditions.
The skills crisis
Another issues where Darchis says his team have been attempting to stay ahead of the curve has been in grappling with France’s severe construction skills shortage.
According to France Travail’s Manpower Needs Survey, an average of 64.4% of contractors working on 42,490 projects across the country reported that they were experiencing difficulties in finding skilled workers for construction projects.
Darchis says that over the past five or six years, Eiffage Construction has accelerated its human resources policies with a series of loyalty programmes and new training schemes aimed at retaining current employees and attracting new ones.
“We noticed a significant shift in the recruitment process compared to 10 years ago. Now, it is not about us choosing the right candidates, but also about us being attractive to potential employees,” he says.
“This proactive approach has helped us avoid delays in our construction projects due to a lack of skilled construction managers or workers. We have not encountered any such problems in France, but we have taken proactive measures to prevent them. Our network of partner companies, state bodies, and subcontractors has also played a significant role in ensuring the successful completion of our construction projects. Overall, maintaining a precise and proactive approach to monitoring and addressing workforce challenges has been crucial for us.”
The opportunities and challenges of technology
One part of the solution, Darchis says, can be implementing new technologies to make work more efficient.
He says that digital processes such as Building Information Modelling (BIM) creates opportunities across the construction industry and beyong by allowing the possibility of building virtually, before real-world construction takes place. That helps when it comes to estimating the needed quantity of materials and equipment for the project.
On the other hand, he says, it is a challenge as the entire supply chain – the architects, design offices and the contractor – have to work in the same way using a BIM collaboration platform in the perspective of having a unitary and shared design workflow.
“We have a challenge in catching up and accelerating the deployment of BIM on our projects, especially the small ones,” he says.
Looking ahead, Darchis also adds that Eiffage is looking at the potential for using artificial intelligence in its business model.
“It makes us think about the potential of AI in the act of building and especially in the act of designing. It’s a real challenge, an opportunity surely in the medium-term, but a challenge to master it well.”
CONTÁCTESE CON EL EQUIPO
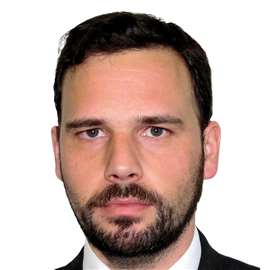