Especial mantenimiento: Equipos a tono
24 March 2022

No es ningún secreto, un aspecto esencial para que un equipo funcione correctamente es su mantenimiento. El cuidar un equipo como es debido (ya sea una impresora, un automóvil o un gran equipo de construcción) es de suma importancia para que éste preste un servicio eficiente y alcance la productividad que se espera de él. Pero, aunque suene de perogrullo, no siempre las empresas cumplen con las especificaciones de los fabricantes y someten a sus equipos a esfuerzos indebidos. En este sentido es que Construcción Latinoamericana conversó con algunos ejecutivos de la industria para saber más sobre cómo se debe proceder para un correcto mantenimiento de un equipo de construcción.
Horas de uso
Por supuesto que cada fabricante tiene puntos específicos de inspección, que son generalmente, medidos a través del horómetro de la máquina. Sin embargo, Vladimir Machado, especialista de producto de Link-Belt Latin America, resume que existen indicadores generales. “En las inspecciones diarias, es necesario chequear los niveles de fluido, drenar el pre-filtro de combustible y chequear el filtro de aire, hacer la limpieza del material rodante y la inspección visual de los rodillos, verificar las mangueras del equipo y hacer la lubricación de los puntos, según la orientación del fabricante. En el caso de Link-Belt, como tenemos un sistema de lubricación extendida en puntos importantes, como brazo y pluma, es necesario hacerla cada 1.000 horas”.

El ejecutivo comenta además que “cada 500 horas, se debe lubricar la corona de giro y rodamiento de la mesa, cambiar el aceite del motor y los filtros de combustible y del motor. Cada 1.000 horas, es necesario lubricar el sistema de brazo y pluma, cambiar el aceite del reductor y del engranaje de giro, los filtros de aire de la cabina, además de los ítems diarios”.
Por último, cada 5.000 horas, además de los ítems a verificarse e inspeccionarse anteriormente, es necesario cambiar el aceite hidráulico. “Pero siempre recordando que hay otros puntos que constan de los manuales de los distintos fabricantes y que deben ser incluidos y contemplados, según la recomendación”, dice.
Para las máquinas de Liebherr, las horas de funcionamiento marcarán el ritmo, dice Robson Bosco, Supervisor de Asistencia Técnica, para Movimiento de Tierras, en Liebherr Brasil. “Dependiendo de ellos, se deben diferentes planes de inspección. El tiempo medio entre fallos (MTBF) y el tiempo medio de reparación (MTTR) también son KPI que los clientes suelen tener en cuenta para medir la calidad del mantenimiento. MTBF ayudará a medir la confiabilidad de la máquina, mientras que MTTR medirá cuánto tiempo llevará repararla”, comenta.
Entorno
Pero si las horas son el principal indicador, no se puede ignorar la aplicación y el entorno en el que opera una máquina. Hay algunas condiciones en el lugar de trabajo que pueden causar tensión adicional en la máquina, lo que puede requerir un programa de mantenimiento más estricto. “Situaciones como alta contaminación por polvo, escombros, proximidad a la sal o materiales abrasivos son solo algunos de los factores que se deben considerar y monitorear al marcar el programa de mantenimiento adecuado para un activo o flota”, recuerda Jahir Echevers, system application specialist de Caterpillar.

Según indica el ejecutivo, hay tres elementos fundamentales antes de la mantención de una máquina. “Control de contaminación: en un taller, los contaminantes pueden afectar gravemente la durabilidad de una máquina, especialmente cuando se manipulan componentes hidráulicos. La configuración y las herramientas adecuadas para el taller son fundamentales; personal capacitado: un equipo de servicio puede hacer o deshacer el éxito general en el lugar de trabajo. Tener un personal de servicio debidamente capacitado es esencial y no digo solo capacitación a bordo, sino aprendizaje continuo sobre los últimos productos, procedimientos, herramientas disponibles y medidas correctivas junto con las pruebas; y calidad de partes y fluidos: el diseño y la calidad de una pieza de repuesto es clave para cualquier mantenimiento”, explica. “En Caterpillar, realizamos pruebas exhaustivas en nuestras piezas de repuesto recomendadas en las condiciones más duras para garantizar que los clientes tengan sus activos en funcionamiento”, añade.
Caterpillar ha invertido en investigación y desarrollo para obtener más horas de piezas mientras mantiene altos estándares de calidad. “En algunos casos, hemos aumentado la vida útil de algunos filtros con nuestra línea “Next Gen” que ahora utilizan la mayoría de nuestras máquinas más nuevas”, comenta.
Conectividad
La funcionalidad del equipo es sin duda un factor clave, porque una de las principales preocupaciones cuando una máquina necesita mantenimiento es precisamente cuánto tiempo estará fuera de circulación. En este sentido destaca la tecnología Expert Alerts ofrecida por John Deere. Thomás Spana, sales manager de la división de construcción de John Deere Brasil, explica que “consiste en alertas que ayudan a identificar, a través del análisis de datos, y diagnosticar situaciones en las máquinas antes de que muestren signos de falla, lo que permite que el propietario continúe operando temporalmente hasta un momento conveniente, minimizando así la reparación, costo y el impacto potencial en los componentes de la máquina. Este es un sistema proactivo en el que se notifica al distribuidor sobre posibles inquietudes y luego debe trabajar con el contratista para garantizar que la máquina esté en servicio durante la mayor cantidad de tiempo, con un impacto mínimo en la operación o el resultado final”.
Spana también destaca que John Deere también tiene productos que mejoran el tiempo de actividad de la máquina y buscan minimizar el tiempo de inactividad tanto como sea posible. “John Deere ha invertido mucho en conectividad, un punto clave para que procesos que alguna vez fueron comunes se vuelvan innovadores e inteligentes. A través de dicha conectividad, los clientes pueden preocuparse menos por el tiempo de inactividad del equipo, lo que puede significar una pérdida de tiempo y dinero. Con su plataforma Precision Construction, la empresa permite que sus distribuidores diagnostiquen los problemas de las máquinas de forma remota, sin tener que enviar un técnico al lugar de trabajo, lo que reduce significativamente los costos y el tiempo de inactividad. Los distribuidores pueden incluso actualizar el software de la máquina a larga distancia, así como leer y borrar códigos de falla y guardar y compartir los datos de rendimiento de la máquina”.
El monitoreo de todos los diferentes datos que provienen de las máquinas se ha convertido en una parte vital para administrar con éxito una flota. Echevers comenta que con Cat VisionLink, los administradores y propietarios de flotas pueden monitorear la utilización y el estado de salud de todos sus activos de forma remota. “Además, pueden llevar un registro de sus mantenimientos e inspecciones realizadas con Cat Inspect, ver las piezas necesarias para su próximo mantenimiento y comprarlas a través de internet. Caterpillar hace que sea más fácil que nunca administrar la flota sin importar en qué parte del mundo se encuentren los clientes”, finaliza.
En términos de datos Bosco comenta que desde el centro de control / centro de gestión de flotas de Liebherr puede recibir datos importantes de la máquina. “Estos datos que llegan a tiempo pueden proporcionar acciones correctivas rápidas y asertivas con respecto a la recuperación de la máquina, ahorrando así dinero y tiempo durante las paradas inesperadas”, asegura.
CONTÁCTESE CON EL EQUIPO
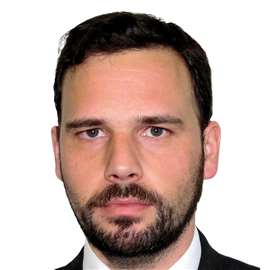