3 things we learned from Trimble Dimensions
19 November 2024
US-based construction software and technology equipment provider Trimble recently held its annual user conference – Trimble Dimensions – in Las Vegas, US. Even though the company counts some of the world’s largest OEMs and contractors among its clients and customers, the weeklong conference highlighted how even the smallest construction firms can take advantage of today’s biggest tech.
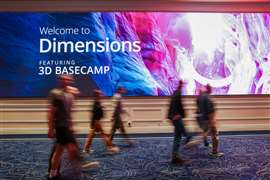
From new solutions for ‘old-reliable’ construction equipment to an emphasis on improving workflows, the construction technology sector is becoming more accessible and affordable for everyone.
Here’s three things we learned at Trimble Dimensions:
1) Fitting technology to the right construction equipment
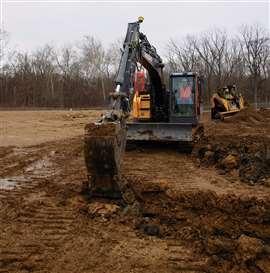
Early in the construction technology evolution, machine-automation features and products (like grading assist or automated geospatial services) were often developed for and affixed to the biggest equipment: cranes, excavators and mining trucks being some of the first and more productive receivers of advanced technology.
But over time, firms have found their tech products too often ended up exclusively attached to equipment outside smaller contractors’ price ranges or to units those firms do not regularly use.
Steven DiBenedetto, a product manager for Trimble’s field solutions software division, told Construction Briefing this reality inspired a shift in attention.
“We recently announced the availability of a solution that is available for compact track loaders [CTL],” DiBenedetto said at Dimensions, referring to Trimble’s Siteworks Machine Guidance system. The inclusion of Siteworks on CTLs was announced the week prior to Dimensions.
“We’re looking to really start to help our contractor friends in the smaller contractor space,” DiBenedetto said.
The Siteworks programme includes a Trimble SPS986 or a Trimble R780 GNSS Smart Antenna with tilt compensation and the Trimble ProPoint positioning engine, along with any bring-your-own-device or Trimble field tablet that supports the Siteworks software.
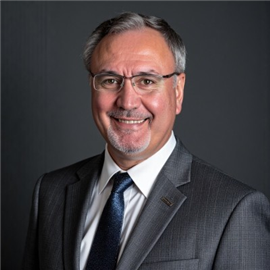
“The module enables contractors to use Siteworks off the machine to design, measure and layout projects,” said the company. “Contractors can then transfer the GNSS receiver and field tablet from the pole to the compact track loader… to provide in-cab, 3D machine guidance and grade checking capabilities without the need for a surveyor.”
DiBenedetto acknowledged new tech in general can be overwhelming to implement for even experienced construction crews, which is why the focus has been on putting workflow products like Siteworks on machines smaller contractors own or rent regularly.
“We are putting a lot of emphasis on the workflows themselves, trying to make it as easy as possible to start getting into Trimble technology,” he said, noting modern surveying and geospatial products have become “super accurate, super precise”.
When coupled with a software designed to make jobs easier, DiBenedetto said customers typically adjust rather quickly.
He added, “A lot of times, that comes with a fair bit of complexity, and that is a hurdle for these contractors to get into. So, guided workflows, those sorts of things, can allow people who might be technology afraid… to not have that fear of jumping in.”
2) Continuously connected construction powered by AI
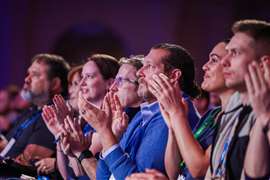
But advanced tools for compact track loaders is just one step.
Jon Fingland, a Trimble vice president and building category general manager explained for Construction Briefing how smaller firms that have not updated their technological approach in the last decade can catch up quickly.
They are focused on companies that have some of the highest construction costs in the industry, Fingland said, with materials and labour making up the bulk of those costs. “It’s where, if you make an error, there’s a lot of rework, and the cost is high.”
Fingland believes once construction crews like these make the jump into connected workflows, they’ll realise the long-term cost savings, particularly within sectors where material and labour can be higher than average.
He noted, too, that Trimble has leaned into a subscription-based model for most of its offerings, which allows companies to budget month-to-month instead of paying outright for the services.
3) ‘Seeing the full story come together’
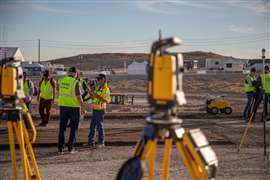
Ultimately, construction’s major tech players have all (mostly) been on the same page regarding their innovative projects: the more they can work together, the better the industry will be.
This means that more tech firms than ever are relying on ‘open’ or ‘free’ launches of their software so that contractors and project managers of all sizes can find the right combination of solutions.
From Trimble’s perspective, it means their software needs to communicate with competitors like Leica Geosystems, Hexagon Geospatial, or Esri, because the company can’t demand its mid-sized and smaller clients abandon prior technology investments.
Nathan Patton, a product marketing manager of construction tech at Trimble, says that whether a contractor invests entirely into one company’s suite of products or uses a mix-and-match approach doesn’t matter.
“People call it the golden thread that connects you through from field all the way through to your budget, your schedule,” Patton told Construction Briefing.
Aiding the construction storytelling process has been the advanced leaps in reality-capture tech, Patton said. From use of drones to advanced scanners and photogrammetry to real-time modelling, the data created from these processes is getting easier to create, disseminate, categorise and share among stakeholders.
“Trimble Connect, our cloud platform, brings the ability to support complex, massive files like point clouds and reality-capture data,” explained Patton, who said the next step in the process is key. “This makes it easier for contractors… to tie it into actual downstream workflows.”
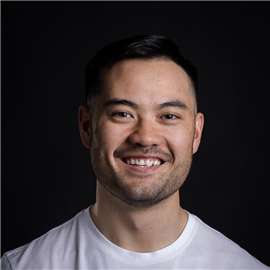
He noted Connect now works with scanning platforms that can be installed to phones or tablets, a huge development for smaller contractors who previously would have had to invest in additional (and pricey) purpose-built processors.
“You can take a scan with your iPhone,” explained Patton. “That data flows seamlessly into Connect and funnels into our project management software.
“To finally unlock that value of reality capture has been, for sure, the biggest thing this year.”
Looking ahead, Patton, Finland and DiBenedetto all shared an acute optimism about the future of construction technology.
Patton perhaps summed it up best.
“It’s about democratising,” he remarked. “It’s about getting people together and communicating. When I’m talking to our customers in the field asking these questions, they’re so ecstatic about it because they’re able to bring data to the table and not problems.
“They’re able to come to the table and have a conversation and get away from some of that stigmatised version of construction with this argumentative and combative [nature].
“Instead, it’s like we have this shared view of the world: How do we collaborate and build better communities together?”
CONTÁCTESE CON EL EQUIPO
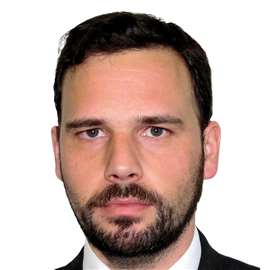