Camiones rígidos y articulados
03 July 2020
Desde una edad temprana nos encantan los camiones de volteo y a medida que crecemos, y envejecemos, el encanto se transforma en enamoramiento. Algo tiene de alucinante ver un camión transportar carga del punto A para luego volcarla en el punto B, sea la carga tierra, rocas, basura, material de desecho o arena.
Existen muchos tipos de camiones y en este artículo hablaremos de aquellos camiones que fueron específicamente diseñados para trabajar fuera de carretera. De estos camiones existen dos tipos: aquellos que tienen bastidor rígido, y aquellos que tienen un bastidor articulado - que realmente tienen dos bastidores unidos por una junta oscilante.
Un poco de historia
Cuando hablamos de fabricantes de camiones rígidos, el más conocido de sus pioneros es Euclid, empresa originalmente establecida en el estado de Ohio, en Estados Unidos y específicamente se reconocen los avances de su fundador: George Armington Jr. La empresa Euclid fabricó su primer camión de volteo con accionamiento hidráulico en el año de 1930 y a partir de ahí Euclid siguió produciendo modelos que se superaban en capacidad de carga, velocidad, y sistemas que permitieran esta mayor velocidad sin sacrificar la seguridad y por supuesto, el confort del operador. El objetivo final era claro: reducir el costo por tonelada.
Euclid fue eventualmente absorbida por General Motors para posteriormente venderla en 1968 obedeciendo las leyes antimonopolio de los Estados Unidos y, a partir de ahí, fue propiedad de varias empresas: White Motor Corporation, Daimler Benz, Clark Michigan, al consorcio VME (Volvo-Michigan-Euclid) y hoy pertenece a la japonesa Hitachi Construction Machinery.
Fue tal la cantidad de camiones rígidos Euclid que GM vendió en las décadas de 1950 y 1960, que en muchos sitios la palabra Euclid fue, y aún sigue siendo, el sinónimo de camión rígido.
Los camiones articulados tienen una historia más reciente y su origen obedece a un proyecto donde los camiones tradicionales no podían funcionar. Su origen se remonta a la década de 1950 cuando la empresa sueca Volvo BM encargo a la también sueca Lihnells Vagn AB (Livab) el desarrollo de un vehículo especializado para obras donde las condiciones de terreno eran poco ideales. Este diseño original de un volquete arrastrado por un tractor evolucionó de tal forma que en 1966 Volvo lanzó al mercado el DR631, que vino a ser el primer camión articulado fabricado en serie. Eventualmente Volvo compro a Lihnells Vagn AB.
Que se ofrece en el mercado
La tecnología utilizada en los camiones rígidos y articulados es muy similar. Con excepción de los territorios de países europeos o de Estados Unidos, en América Latina ningún país requiere todavía las normas Tier 4 o su contraparte europea en los equipos fuera de carretera, por lo cual los fabricantes ofrecen versiones con motores que cumplen con niveles de emisiones Tier 2 o Tier 3 según sea el caso.
Ambos tipos de camiones utilizan sistemas de monitoreo remotos, de carga útil, sistemas telemáticos, y retardadores automáticos, controles de tracción, de velocidad de descenso, advertencias de colisión, etc.
Los avances que se han incorporado tienen el objetivo de reducir el costo por tonelada, mejorar la comodidad del operador y reducir la injerencia de éste en la toma de decisiones. Es muy importante que el operador se sienta cómodo y que la operación sea sencilla, porque son equipos que pueden llegar a costar varios millones de dólares y su impacto en el ciclo total de producción es alto.
Ni el camión rígido ni el articulado son auto cargables, como lo son las mototraillas y parte la de la elección entre uno y otro depende de la herramienta que se utilice para su llenado.
La aplicación marca la elección
La aplicación es la que define la elección entre camiones rígidos y articulados y los factores que más influyen son el tamaño, la herramienta de carga – llámese excavadora, pala o cargador sobre ruedas -, la cantidad y tipo de material a mover, y especialmente las condiciones del lugar de trabajo.
Salvo muy pocas excepciones, las condiciones del suelo dictan qué tipo de camión se debe utilizar en un sitio de trabajo determinado. Los camiones articulados pueden operar en la mayoría de las condiciones, pero cuando estas condiciones son menos que las ideales es cuando son necesarios.
Si el terreno es húmedo, fangoso, blando, arenoso, resbaladizo y de poca capacidad tracción, bien tenga una de estas condiciones, una combinación de ellas o todas ellas, el camión articulado es la mejor opción.
Los camiones articulados vienen equipados con sistemas de tracción en las seis ruedas – o 4 x 4 en algunos modelos – y con neumáticos anchos, de alta flotación que se adaptan al entorno y proporcionan al equipo la capacidad de maniobrar en condiciones extremadamente deficientes, incluso en la total perdida de tracción, el sistema de dirección y la junta oscilante entre sus dos bastidores le permite hacer el “paso del pato” y salir de situaciones de atascamiento.
Los camiones articulados son más livianos que los rígidos y se equipan con neumáticos anchos que hacen que tengan una baja presión sobre el suelo, por lo cual el articulado no requiere de caminos bien compactados ni regulares, como si los requiere el rígido.
El camión articulado no requiere de rutas planas, ya que su tipo de suspensión y el diseño del ángulo de ataque del bastidor delantero le permite sortear terrenos irregulares.
Otra de las ventajas del camión articulado es la ruta de acarreo. El camión articulado se desempeña bien en lugares donde al transportar la carga se encuentren giros bruscos o existan limitaciones en el radio de giro, carreteras estrechas, pendientes y limitantes de alturas y en general que el tamaño del proyecto no permita la adecuación y mantenimiento de una carretera. El camión articulado, por su menor presión sobre el suelo, causa menor perturbación sobre el mismo, por lo cual se adaptan particularmente bien al desarrollo de sitios pequeños donde es difícil o prohibitivo hacer caminos de acarreo.
La maniobrabilidad de los camiones articulados es un aspecto muy importante. No solo tienen seis ruedas, sino que están diseñados para que las seis estén en contacto constante con el suelo, que además de permitirle funcionar en lugares de pobre tracción, también le permite trabajar en pendientes de hasta 35% y resistencias de rodadura de hasta 20%.
Cualquiera sea el fabricante que elija para suplir sus necesidades, todos ellos han incorporado avances en sus diseños para mejorar la tracción. Desde bastidores inclinados que distribuyen peso hacia adelante para utilizar mejor la tracción 6x6, pasando por controles de tracción ya incorporados en los equipos para proporcionar tracción optima en todas las etapas de la ruta de acarreo, sistemas que monitorean constantemente el deslizamiento de las ruedas y que dependiendo de la dificultad del terreno pueden activar automáticamente los embragues de los ejes traseros y/o modular los frenos de manera que la potencia se transfiera a la rueda que tiene tracción.
Todos estos sistemas facilitan la operación y se traducen en un menor consumo de combustible, menor tiempo de ciclo, mayor vida útil de los neumáticos y permiten al operador concentrarse en la maniobra, haciendo de esta más segura y eficiente.
La sobrevivencia del más apto
Las mototraíllas o motoescrepas eran los equipos que más se utilizaban para mover tierra hasta la década del ‘90. Este tipo de equipo ha tenido un repunte recientemente, y dadas ciertas condiciones pueden ser el método menos costoso para mover tierra, pero el camión articulado la ha sustituido en muchas aplicaciones y es cada vez más popular. Y es que hay un factor que juega a favor del camión articulado: se adapta prácticamente a todas las condiciones de terreno y por eso son tan útiles y cada vez más populares. Adicionalmente, el nivel de pericia que se requiere para operar una mototraílla es mucho mayor que el requerido para operar un camión.
En la minería a gran escala la presencia del camión rígido sigue siendo y será importante. Lo que ha cambiado es que los camiones articulados son cada vez más frecuentes en las minas debido a su versatilidad. Para que una mina pueda operar, necesita construir rutas que lleguen a nuevos frentes, preparar terrenos para diferentes maniobras, hacer proyectos de recuperación según dicte la obra o las regulaciones locales, y muchas operaciones más. Es aquí donde la versatilidad del camión articulado lo hace tan popular.
La lista de aplicaciones es amplia. Se utilizan en proyectos de desarrollo de viviendas e industriales, estanques de contención y carreteras a todo lo largo de América Latina. En minas de sal marina en Venezuela. Panamá fue el líder de ventas en camiones articulados en toda América Latina durante la ampliación del Canal. Costa Rica es un consumidor asiduo de articulados debido a la alta precipitación de lluvia anual, la que hace prohibitivo el uso de otro tipo de camiones en ciertos proyectos durante la estación más lluviosa. Mas no es necesario que llueva mucho para que el articulado sea ideal, como es el caso del norte de México, donde cada vez son más populares debido a la minería de mediana escala – y lo son también en esta misma aplicación en América Central en ambientes mucho más húmedos -. El camión articulado es ya tradicional en Chile en labores de apoyo en la alta minería o en acarreando sal en minas al norte del país, concepto que ha sido copiado recientemente en minas de sal en las alturas de Bolivia. Colombia fue por mucho tiempo líder en ventas en camiones articulados de baja capacidad y se experimentó con los articulados en el transporte de la caña de azúcar en el Valle del Cauca, al adaptarse el chasís delantero de un articulado a un tren de remolques para acarreo de caña.
El camión articulado se adapta y es una buena opción para mover material desde lugares pequeños hasta lugares de excavación masiva, sin importar que las condiciones del terreno sean ideales o no.
La popularidad del camión articulado en América Latina no ha avanzado al mismo nivel que en países más desarrollado debido a factores locales, especialmente sociales y económicos. En el primer caso, existen restricciones laborales en algunos países que obligan al uso de los camiones de carretera y en el segundo caso, la adaptación de tolvas de hasta 60 toneladas de capacidad en camiones de carretera que, aunque no tienen la misma durabilidad o capacidad que los equipos diseñados para ese fin, su bajo costo es a menudo decisivo al momento de la selección especialmente en aplicaciones de construcción, canteras y minería de pequeña escala.
Pero cuando la cantidad de material que se debe mover es muy grande, es cuando los articulados se ven superados por los rígidos debido a que la combinación de carga y velocidad de estos últimos proporciona un mejor costo por tonelada.
La ventaja está en el volumen
Las minas de superficie son inversiones a largo plazo donde se establecen rutas de acarreo que son bien definidas, compactadas, tienen buen drenaje y son bien mantenidas. En esta aplicación los camiones rígidos son la mejor opción. Al igual que el lugar donde trabajan, los camiones rígidos son de mayor precio y de vida más larga.
El camión rígido es más pesado, de tracción trasera y requieren de rutas de acarreo compactadas, bien mantenidas y con buen drenaje. Estos equipos rinden mejor cuando las pendientes son menores a 15%, siendo lo ideal rutas planas, distancias largas donde el camión pueda desplazarse a gran velocidad transportando gran volumen de carga. El camión articulado puede hacer rutas largas, pero lo ideal es que no sean mayores a 3.500 metros ya que más allá de eso, el desgaste resultará excesivo.
Los camiones rígidos se utilizan en los trabajos donde se requiere transportar gran carga útil, a mayor velocidad que equivale a ciclos más cortos y por consiguiente menor costo de posesión. Dicho de otra manera, la ventaja que tienen los camiones rígidos sobre los camiones articulados es su capacidad de carga. La desventaja es que la mina u obra requiere hacer inversiones mayores en las rutas de acarreo.
En líneas generales los camiones articulados están disponibles en capacidades de transporte que van de desde las 18 hasta 55 toneladas métricas. Las capacidades de los camiones rígidos van desde las 38 hasta las 450 toneladas métricas. Es de destacar que los camiones articulados se clasifican por su capacidad de carga en toneladas cortas, es decir 1 tonelada igual a 2000 libras y la nomenclatura de los fabricantes usualmente incluye la capacidad en toneladas cortas en el modelo del equipo.
La regla empírica de la maquinaria fuera de carretera es que, para los grandes movimientos de tierra, los equipos más grandes nos pueden generar economías de escala, acarreando mayor carga a un menor costo por tonelada. El reto siempre ha estado en que, cuanto más grandes y pesadas son las máquinas, suelen perder la versatilidad que ofrecen las maquinas más pequeñas. Es por ello que un equipo que conserve su versatilidad al aumentar su tamaño siempre puede ofrecer grandes beneficios.
El mercado de América Latina
Camiones Articulados
El mercado de América Latina consume entre las 120 a 170 unidades anuales incluyendo a Brasil. Por tipo de camión, el segmento de más de 36 toneladas métricas es el líder con un 65%. Por país Chile, México, Colombia y Panamá consumen el 70% de todos los camiones articulados.
Los fabricantes activos en la región son Bell, Caterpillar, Doosan, John Deere, Komatsu, Terex y Volvo.
Camiones Rígidos
El mercado de América Latina consume entre las 220 a 250 unidades anuales incluyendo a Brasil. Por tipo de camión, el segmento de más de 275 toneladas métricas es el líder con un 30%. Por país Chile, México y Perú consumen el 80% de todos los camiones rígidos.
SOBRE EL AUTOR
Cesar Muino es Ingeniero Mecánico graduado de la UCV en Venezuela y tiene más de 25 años de experiencia en la industria de equipos de construcción en el mercado de América Latina.
Caterpillar: Hito en automomía
El mayor fabricante de equipos pesados en el mundo tiene una fuerte presencia en lo que son los camiones de carga, sean rígidos o articulados. Pero además de sus modelos, en estos días Caterpillar celebra un hito de su sistema de conducción autónoma de camiones rígidos. Este año se completó el transporte de 2.000 millones de toneladas de material por camiones equipados con el sistema Cat Command.
El sistema da la posibilidad de conducir el camión remotamente. Desde que los primeros seis camiones con este sistema fueron aplicados en 2013, la solución creció y hoy en día es utilizada en una flota de cerca de 250 vehículos de minería.
Mineras de todas las partes del mundo aplican el Cat Command para camiones rígidos. El sistema puede venir de fábrica en sus modelos de camión rígido, pero, además, puede ser incorporado a través de kit de retrofit en los modelos 789D y todos los modelos de numeración 793, 794, 796, 797 y 798. Por fin, el Cat Command también puede ser aplicado en el modelo 930E, de Komatsu.
Dentro de los más recientes contratos firmados entre Caterpillar y empresas mineras para operación remota de camiones rígidos, dos de ellos son en América Latina. La empresa Teck Resources recibirá camiones 794 AC con el sistema para operar en la Fase 2 de la mina Quebrada Blanca, al norte de Chile. Por su parte, Anglo American también utilizará camiones 794 AC con el Cat Command en la mina de Quellaveco, en Perú.
Volvo: padre de los articulados
Volvo Construction Equipment, la marca creadora del concepto de camión articulado, tiene el modelo de mayor capacidad de carga entre todos los articulados: el A60H, que puede llevar 55 toneladas métricas de material. Sin embargo, la línea completa tiene otros modelos muy populares en la serie G, anterior al A60H.
La serie tiene los siguientes modelos: A25G (capacidad de 24 toneladas métricas), A30G (29 toneladas métricas) y A45G (41 toneladas métricas).
Hoy las novedades de la marca están en el sistema Co-Pilot, que es un integrador de funcionalidades de operación. “El Co-Pilot es como si fuera una tablet, y los demás sistemas son las aplicaciones”, dice Boris Sánchez, gerente regional de soporte a ventas de Volvo CE Latin America. El software de control para los ADT de Volvo es el Haul Assist, que permite entre otras cosas pesar la carga instantáneamente a través de sensores. Esto hace que el operador de un camión Volvo pueda estar siempre cerca la carga nominal, por lo tanto, respetando el límite del equipo sin dejar de optimizar la productividad.
Más recientemente, Volvo ha desarrollado y lanzado otras aplicaciones para funcionar dentro do Haul Assist. Una de ellas es el Map, que permite al operador conocer la ubicación de todos los demás camiones conectados en un sitio de trabajo. Con esta información, el usuario puede usar otra aplicación del Haul Assist que es el Speed Advice. Con esto, si por el Map un camión recibe la información de que hay una fila para descargar, con el Speed Advice recibe una sugerencia de velocidad óptima para no generar pérdidas.
Otras aplicaciones del sistema incluyen el Cruise Control (piloto automático con velocidades pre definidas), y el Downhill Speed Control (que controla la velocidad pre definida en pendientes).
La decisión de Volvo CE fue incorporar de fábrica el sistema Co-Pilot en todos los camiones articulados. De manera que vienen con el Haul Assist y funcionalidades de pesaje automática, mientras que sistemas como el Map, Speed Advice, Cruse Control y Downhill Speed Control son opcionales.
Liebherr: tracción diésel-eléctrica
Son ya dos los camiones rígidos Liebherr T 236 en aplicación en el mundo, uno en Sudáfrica y otro en Austria. El equipo, lanzando en 2016, cambió el panorama de este mercado al incorporar la tecnología diésel-eléctrica para la tracción, lo que es muy raro en el transporte de carga minera para la clase de 100 toneladas, como se sitúa el T 236.
La gran ventaja presentada por el fabricante alemán se relaciona con el comportamiento del camión en pendientes. Según la empresa, el accionamiento eléctrico, combinado con la motorización diésel, permite vencer pendientes más inclinadas. Esto podría significar una adaptación más fácil a la geología y a la topografía natural del yacimiento. Además, los cambios de marcha con este sistema no producen movimientos brutos en el chasis, lo que contribuye para evitar derrames de material.
Pero quizás el más importante diferencial del T 236 y su sistema híbrido de accionamiento es la tecnología Litronic Plus Generation 2AC. Con este sistema de control electrónico de la tracción, la potencia transmitida a las ruedas es permanente, deshaciendo el efecto natural de pérdida de velocidad en pendientes hacia arriba. Obviamente, con un sistema diésel convencional eso se compensa con más tracción, al mismo tiempo con mayor consumo de combustible.
Liebherr ha integrado en el modelo T 236 el sistema Trolley Assist, que incorpora pantógrafos de transmisión eléctrica a las ruedas. Este sería el responsable por hacer llegar la energía extra enviada por el sistema Litronic al percibir que está en pendiente hacia arriba.
Mientras promueve su modelo diésel eléctrico, Liebherr ya prueba un nuevo prototipo. Se trata del TA230, que está en fase de prueba en terreno. Pero las pruebas hechas son tan exigentes que la empresa optó por no poner un conductor adentro. Desarrolló un sistema de conducción semi autónoma remota, para llevar el camión al límite en el campo de pruebas de Kirchdorf, Austria. Videos de estas pruebas pueden ser vistos en nuestra edición digital.
Bell: la evolución sudafricana
La nueva generación de camiones articulados del fabricante sudafricano Bell Equipment tiene capacidades de carga variando entre las 18 y 45,4 toneladas cortas. La serie recibe la letra E en la nomenclatura para significar Evolución.
Los nuevos modelos B20E, B25E, B30E, B45E y B50E tienen un nuevo diseño oscilante del chasis y neumáticos de movimiento más elevado, para prevenir el atasco del camión en terrenos demasiado difíciles en minas, canteras y otros sitios donde se los apliquen.
Otra novedad específica para el modelo B45E es la nueva transmisión planetaria. La cabina pasó por rediseño para dejarla más resistente a ruidos externos. Tal como ya es común en todas las categorías de equipos avanzados, los nuevos camiones de Bell tienen un sistema de diagnóstico de problemas exhibidos en pantalla táctil al alcance del operador.
John Deere: Equipos con estilo
Otra compañía que juega un rol relevante en camiones articulados es la estadounidense John Deere. Sus cinco modelos de ADT cubren un rango de capacidad de carga que va desde las 24 hasta las 41 toneladas métricas. En términos de motorización, los modelos John Deere tienen potencias entre 321HP y 481HP.
La marca ofrece al mercado los articulados 260E, 310E, 370E, 410E y 460E. Una característica especialmente interesante en los articulados de John Deere es que su ingeniería ha puesto todos los puntos de mantenimiento diario al alcance del operador desde el suelo. Un ejemplo son los puntos de fijación mecánica que necesitan de engrase diario. En los modelos John Deere, todos se encuentran en un solo lugar. Detalles como este permiten ahorrar un tiempo precioso y poner el equipo para trabajar – y hacer dinero – más rápidamente cuando comienza el día.
La diferencia de ingeniería se nota además visualmente, por la estructura frontal del camión, que en el caso de John Deere es más angosta y ligera que los demás modelos.
Doosan: nuevos lanzamientos
La coreana Doosan sigue disputando el mercado de camiones articulados, con el reciente lanzamiento de los nuevos modelos DA30-7 y DA45-7. Ellos reemplazan los modelos DA30-5 y DA40-5, respectivamente.
Las capacidades de carga de los dos nuevos modelos son: 28 toneladas cortas para el DA30-7 y 41 toneladas cortas para el DA45-7.
En estos nuevos modelos, Doosan profundiza su asociación con Scania, la compañía sueca que le provee los motores para camiones articulados. El DA30-7 tiene potencia de 375 HP, mientras que el DA45-7 tiene 500 HP.
Terex: de tradición
El tradicional nombre Terex Trucks desde 2014 pertenece al Grupo Volvo. Hoy en día, la fábrica escocesa produce dos modelos de articulado, el TA300 y el TA400.
Una nueva transmisión fue incorporada al modelo TA300, y con ella la marca afirma que el modelo mejoró en términos de utilización de combustible, performance, productividad y confort del operador.
Por ejemplo, el modelo incrementó en un 5% su eficiencia de uso del combustible, aumentó su velocidad máxima en 5 km/h y el intervalo de mantenimiento de los aceites pasó de 1.000 horas para 4.000 horas. Y por tratarse de una nueva transmisión, el TA300 tiene ahora ocho marchas hacia adelante y cuatro hacia atrás.
Morooka: carga sobre orugas
El fabricante japonés de dumpers sobre orugas Morooka sigue apostando en sus conceptos innovadores y de nicho. En la última feria ConExpo, la marca presentó dos prototipos que en breve futuro entrarán en producción. Se trata de los equipos MST-4000VDR y MST-200VDR-e.
Según Morooka el MST-4000VDR será el mayor dumper rotacional sobre orugas en el mundo, en tanto el MST-200VDR-e es un modelo totalmente eléctrico de transportador sobre orugas.
Las aplicaciones de los modelos de Morooka son amplias en sus nichos. Se trata de dumpers compactos que transitan con facilidad por terrenos difíciles, por sus orugas, a la vez que tienen buena maniobrabilidad por su tamaño y la rotación de la parte superior en relación con el tren rodante. Es así como tienen buena aplicación en terrenos pantanosos, nieve, obras hidráulicas, actividad forestal y otros nichos.
Mecalac: equipos compactos
Compactos de Mecalac sirven bien para servicios de carga de materiales en ambientes urbanos.
Los dumpers compactos tiene su aplicación en ambientes urbanos, y esta es la especialidad del fabricante francés Mecalac. La marca introdujo este año un nuevo modelo de dumper compacto, el TA3SH.
Con 3,95 metros de largo y 4,41 de ancho, el nuevo modelo de Mecalac tiene su unidad de carga giratoria, y una capacidad de carga de 3 toneladas métricas. De acuerdo con la empresa, esto le hace idóneo para aplicaciones como transporte de hormigón fresco, obras de paisajismo, construcción y reparación de casas y otras situaciones de menores volúmenes.
“Siempre buscamos espacios no tomados en el mercado, y investigamos soluciones innovadoras para atender estas demandas. Este dumper entrega una performance especial debido a su flexibilidad de operación en áreas desafiadoras”, dice el gerente general de Mecalac en Norteamérica, Peter Bigwood.
GHH: diseño innovador
Un diseño absolutamente innovador es lo que presenta el fabricante alemán GHH, que con su modelo MK-42 ha recibido el prestigiado premio al diseño Red Dot Design Award.
Con solo dos ejes, uno para la unidad de tracción y otro para el cargador, el equipo de GHH tiene capacidad de carga de 42 toneladas métricas, volumen de operación entre 19 y 24 m3, un ángulo de descarga de hasta 68 grados, y un radio de giro más cerrado, debido a la división de los chasis en tamaños de largo equivalentes.
Las dimensiones del camión son excepcionalmente compactas, considerando su capacidad: 3.062mm de ancho, 10.535mm de largo y 2.719mm de alto.
La motorización se hace con Mercedes o Volvo, y se puede adaptar el modelo para mercados de emisión regulada en Tier 3 y Tier 4.
CONTÁCTESE CON EL EQUIPO
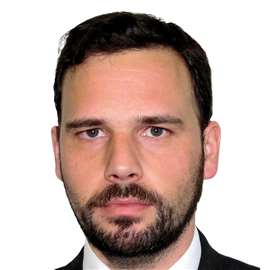